Special casing is a type of pipe fitting used in industrial pipeline systems, typically used to connect pipes of different diameters or shapes to ensure the smooth operation of the pipeline system. The mainstream production processes for other special casings include cold drawing, hot extrusion, forging, welding, etc. These processes can be selected according to different needs and requirements to ensure the production of high-quality special casings.
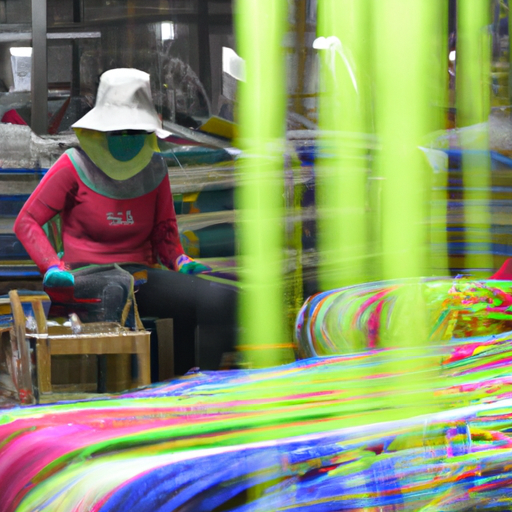
Hot extrusion is another commonly used production process, where metal billets are heated to a certain temperature and then placed into an extrusion machine for shaping. This process allows the metal billet to undergo plastic deformation during extrusion, resulting in the desired shape and size. Hot extrusion is suitable for producing large-diameter special casings, such as large-caliber pipe fittings.
Forging is a traditional production process, where metal billets are placed into a forging machine and pressed into the desired shape and size using mechanical force. This process can increase the density and strength of the metal, while also improving its grain structure. Forging is suitable for producing high-strength and high-density special casings, such as high-pressure pipe fittings.
Welding is a commonly used joining process, where metal billets are welded together to form the desired shape and size. This process can achieve seamless metal connections, while also improving the metal's corrosion resistance and sealing properties. Welding is suitable for producing complex shapes and structures of special casings, such as elbows, tees, and other pipe fittings.
In summary, the mainstream production processes for other special casings include cold drawing, hot extrusion, forging, welding, etc., each with its unique advantages and applications. By selecting the appropriate production process, high-quality special casings can be produced to meet the needs and requirements of different pipeline systems.
Special casing is a type of pipe fitting used in industrial pipeline systems, typically used to connect pipes of different diameters or shapes to ensure the smooth operation of the pipeline system. The mainstream production processes for other special casings include cold drawing, hot extrusion, forging, welding, etc. These processes can be selected according to different needs and requirements to ensure the production of high-quality special casings.
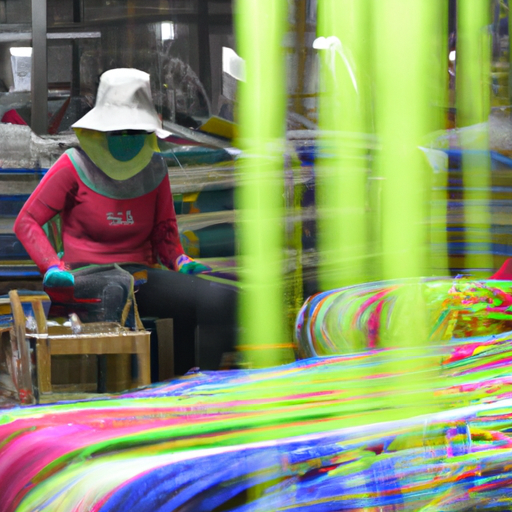
Hot extrusion is another commonly used production process, where metal billets are heated to a certain temperature and then placed into an extrusion machine for shaping. This process allows the metal billet to undergo plastic deformation during extrusion, resulting in the desired shape and size. Hot extrusion is suitable for producing large-diameter special casings, such as large-caliber pipe fittings.
Forging is a traditional production process, where metal billets are placed into a forging machine and pressed into the desired shape and size using mechanical force. This process can increase the density and strength of the metal, while also improving its grain structure. Forging is suitable for producing high-strength and high-density special casings, such as high-pressure pipe fittings.
Welding is a commonly used joining process, where metal billets are welded together to form the desired shape and size. This process can achieve seamless metal connections, while also improving the metal's corrosion resistance and sealing properties. Welding is suitable for producing complex shapes and structures of special casings, such as elbows, tees, and other pipe fittings.
In summary, the mainstream production processes for other special casings include cold drawing, hot extrusion, forging, welding, etc., each with its unique advantages and applications. By selecting the appropriate production process, high-quality special casings can be produced to meet the needs and requirements of different pipeline systems.